Cavitech Applications
Flexible, Clean, Cost Effective
FOWE products are always homogeneous and stable. They can be easily pumped, stored and transported at lower temperatures.
Cavitech technology can be used in multiple applications to emulsify oil based products and improve performance, save money and help minimise pollutants.
Fuel Oil and Bunker Fuels
Oil and Energy Sector Fuel
The best use of Cavitech in an oil refinery is to produce fuel oil-water emulsions for refinery power generation and process furnaces.
The emulsion produced is extremely well mixed and does not require additives to keep it stable. It has lower carbon and sulfur content. It can be combusted in standard fuel oil burners without alterations and, compared to traditional fuels, produces a cleaner burn with lower emissions of NOx and other pollutants.
Cavitech can break down resin formed by polymerization in recirculation loops on storage tanks, to stabilize stored fuel oils and reduce aging.
Cavitech can enhance the characteristics of diesel and jet fuel products as it improves the low-temperature characteristics of middle distillates, reduces particles contaminants and lowers the consumption of chemical additives for blending.
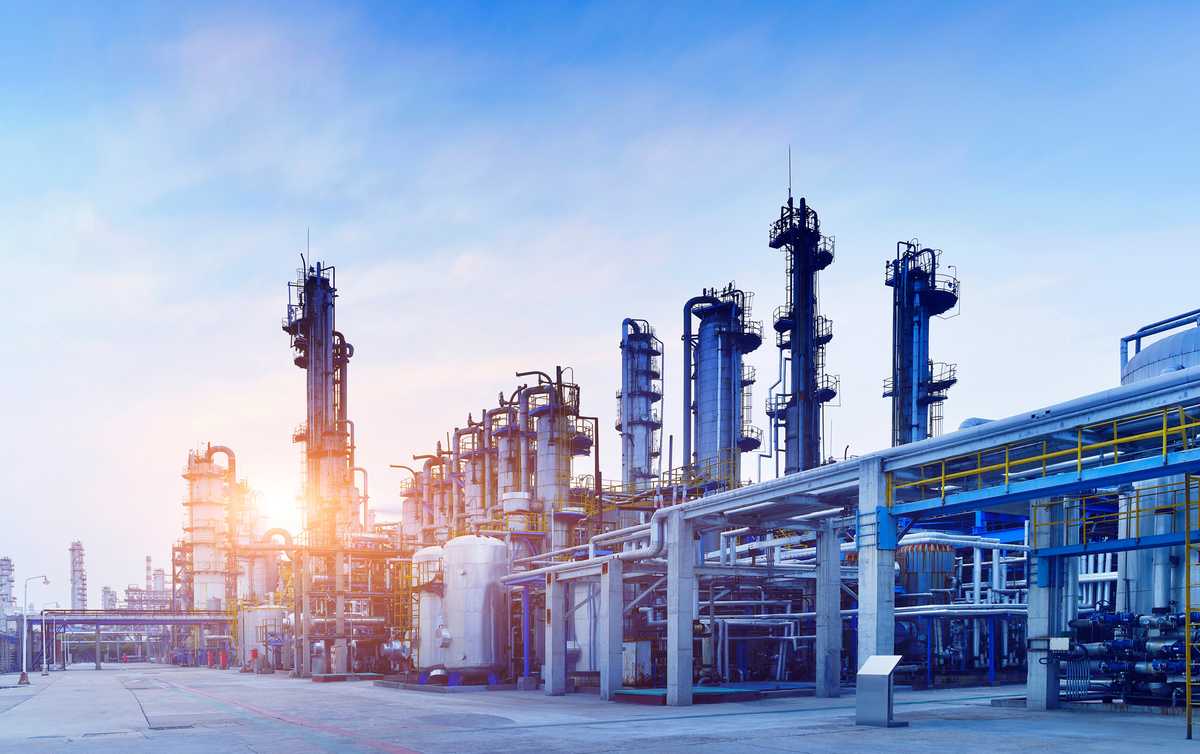
FOWE benefits
- Up to 10% refinery power station fuel savings
- Increased light component conversion
- Reduced cutter viscosity and consumption of diesel
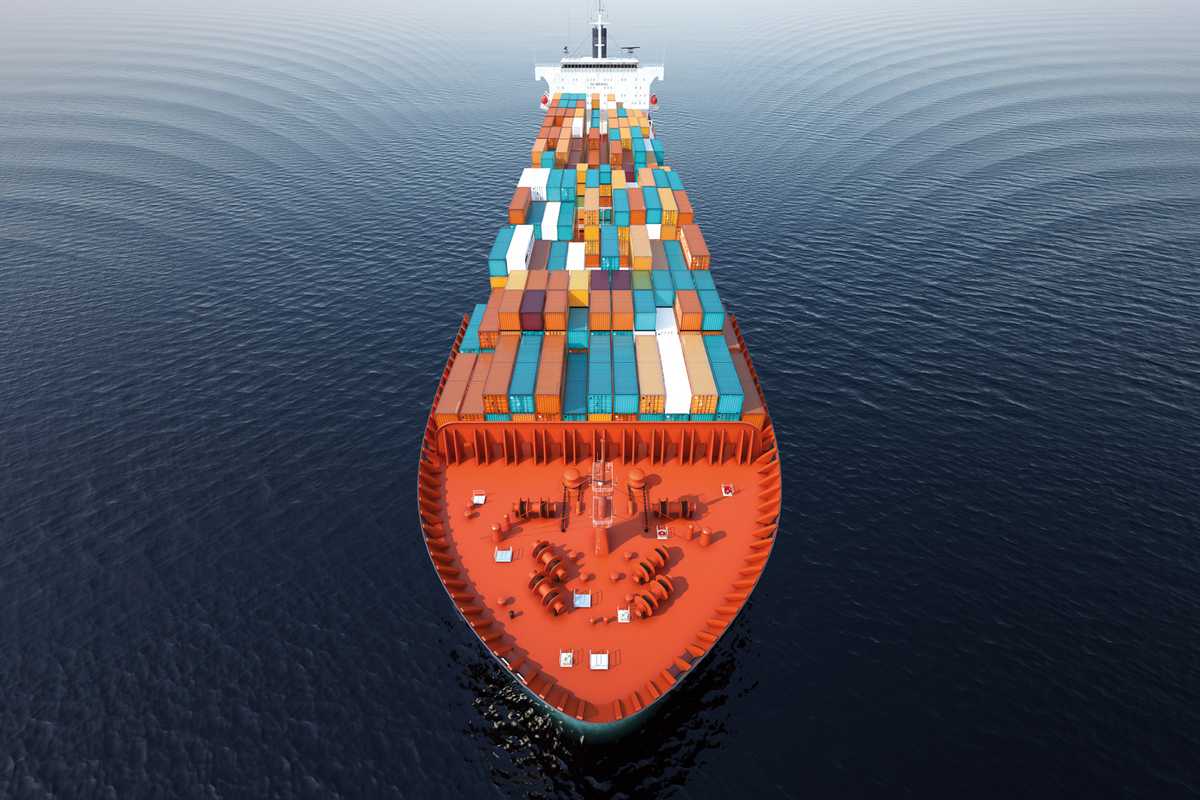
FOWE benefits
- Remains homogeneous and stable
- Improved fuel efficiency
- Reduced NOX emissions
- Better combustion
- Reduced particulate matter
Marine Fuel
FOWE fuels are fully suitable for marine use. The Cavitech system offers important benefits for shipowners. Steam generated from the water-oil emulsion during the combustion cycle reduces exhaust gas emissions and increases the efficiency of the engine, allowing for less fuel to be used.
Particulate matter is reduced, further cleaning the exhaust gas emissions—and even more so when operated alongside scrubbing systems. In seagoing tests, large vessels obtained more than 5% fuel savings and reduced exhaust gas emissions of SOX, NOX, CO2 in line with the International Maritime Organization's regulatory framework.
Oil Refining
Improved Visbreaker and Coker Performance for Better Yields
Making the most of feedstock can offer cost and environmental advantages to refinery operators. When used before the visbreaking or coker process, Cavitech heads—placed in the feedline before heating—provide the following benefits:
- Increased conversion of light components
- Reduced visbreaker residuum viscosity
- Reduced cutter consumption
Real world test data
Measurement | FOWE | No FOWE |
---|---|---|
VBU capacity, t/h | 44,6 | 45,9 |
Feed density, kg/m3 | 1025 | 1028 |
Feed viscosity, cst | 3684 | 3663 |
VBR viscosity, cst | 239 | 292 |
Break viscosity factor | 15,4 | 12,5 |
VBGO draw out, t/h | 2,94 | 2,19 |
VBGO yield, %m/m | 6,59 | 4,77 |
VBB draw out, t/h | 2,15 | 2,00 |
VBB yield, %m/m | 4,82 | 4,46 |
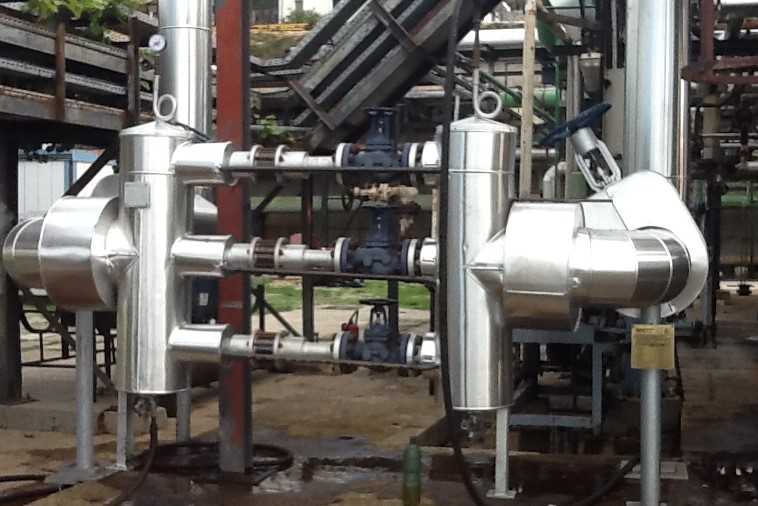
FOWE benefits
- 6,300 tons more gas oil per year ≈ $3.7 million per year
- 1,225 tons more gasoline per year ≈ $700,000 per year
- Higher gas production
- 7,500 tons more diesel and motor gas per year
- Total profit ≈ $3 million per year
Based on a visbreaking unit capacity of 350,000 tons per year
Price assumptions (per ton): gasoil, $600 • gasoline, $600 • visbreaker residue $200
Blending Lubricants

FOWE benefits
- Total homogenization in one in line pass (99.99%)
- Shortened blending time
- Energy saving
- Increased production capacity
- Additive savings
- Compact and safe- no rotating parts
- Reduced maintenance costs
- Suitable for both modern and older mixing technologies
FOWE's Cavitech head is suitable for the production of all types of lubricants. Ensure complete homogenization in just one pass, replacing the role of the traditional blending tanks in the process with just one Cavitech head.
With minimal energy consumption, minimal tanks usage and minimal additive consumption, the Cavitech head produces blends to meet the highest standards in the shortest possible time. Additives are dosed before simply passing at 2 - 10 bars through the head which is the size of a 4" valve. The fully homogenized blend then goes straight into the finished product tanks.
With an automated mixing process, the dosing of the additive into the base oil is continuous throughout the mixing process. The Cavitech head is placed behind the additive dosing point. After passing the components through the head, the product is fully blended to the highest standard and ready for shipment to market.
The great advantage of FOWE's technology is that it can be applied in the most modern blending technologies, as well as in older ones. FOWE's Cavitech head completely replaces the 'blending part' of the lubricant production plant and reduces production costs whilst increasing production capacity.